Lär dig mer om hårdsvarvning
Lär dig mer om hårdsvarvning
Vad är hårdsvarvning?
En vanlig process för bearbetning av härdat stål är slipning där man använder slipskivor av olika form och sammansättning. Vid hårdsvarvning bearbetas materialet med skär som är gjorda av PCBN (Polycrystalline Cubic Boron Nitride) eller keramik. Svarvning av stål som har en hårdhet på 55–65 HRc definieras som hårdsvarvning och är ofta ett kostnadseffektivt alternativ till slipning. Hårdsvarvning ger högre flexibilitet, kortare ledtider och kan även leda till bättre kvalitet på de tillverkade produkterna.
En lönsamhetskalkyl måste alltid göras för att bedöma vilken metod som ger lägst kostnader med hänsyn till produktdesign och seriestorlek. Hårdsvarvning är därmed en kompletterande metod till slipning. Metoden lämpar sig för produkter med komplicerade geometrier och kortare serier. Figur 1 och figur 2 illustrerar skillnaden i skäreggen mellan en slipskiva och ett vändskär som används vid svarvning.

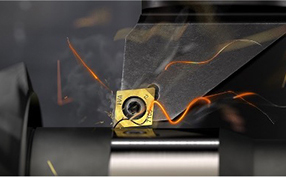
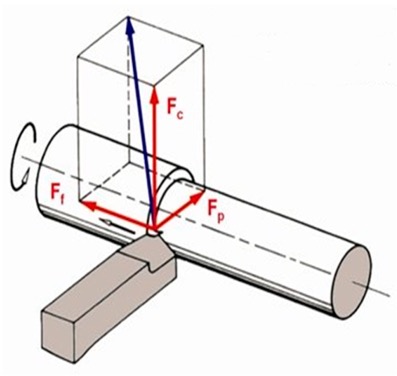
Skärkrafter
Svarvning av stål med en hårdhet av 55 – 65 HRc definieras som nämnts som hårdsvarvning. Men trots att arbetsmaterialet i hårdsvarvning är mycket hårdare än material i mjuksvarvning så innebär det inte att man genererar högre skärkrafter vid hårdsvarvning jämfört med svarvning av icke härdat stål.
Den främsta orsaken till att skärkrafterna blir lägre är de skärdata som används. I hårdsvarvning ansätter man betydligt mindre skärdjup [mm] och matning [mm/varv], vilket ger en mindre spåntjocklek än vid mjuksvarvning..
Det kan nämnas att vid bearbetning av mjukt stål med en hårdhet av ca 200 HB, kan skärkrafterna uppgå till över 2000 Newton. De höga krafterna orsakas av betydligt högre matning och större skärdjup än vid hårdsvarvning.
Flexibilitet
Flexibilitet och lägre kostnader är de största anledningarna till införandet av hårdsvarvning eftersom hårdsvarvning ger betydligt högre flexibilitet än slipning. Den största anledningen till detta är att i en hårdsvarv kan man färdigbearbeta en produkt på ett enklare sätt än via slipning. Vid slipning av produkter med komplicerade geometrier krävs flera specialanpassade slipskivor och i många fall flera olika typer av slipmaskiner i line.
Hårdsvarvning kräver oftast bara en maskin. Alla ytor på produkten kan bearbetas med PCBN eller keramiska skär. Verktygsbyte kan ske automatiskt och det enda som kan behövas är att manuellt vända produkten för att bearbeta ytorna som var inspända i chucken, om inte svarven är utrustad med två chuckar eller en vändstation.
Slipning | Hårdsvarvning |
---|---|
Flera skäreggar med odefinierad geometri. | En skäregg med definierad geometri. |
Lång omställningstid. Slipskiva och anslag måste bytas. | Kort omställningstid. CNC program måste bytas, eventuellt även fixturering och skärverktyg. |
Slipskivans geometri genererar arbetsstyckets geometri. Slipskivan ges rätt form och måste ”skärpas” innan och under användningen. | CNC- programmet genererar profilen på arbetsstycket. |
För olika ytor måste man byta slipskivor eller ha tillgång till flera slipmaskiner för att bearbeta en hel produkt. | Flera ytor kan bearbetas med en skärplatta/skäregg. |
Verktyget, dvs. slipskivan roterar. | Arbetsstycket roterar. |
Restprodukt: slippmull, partiklar från arbetsmaterialet, slipskivan och slipolja. | Restprodukt: spån och kylvätska. |
Ekonomi i hårdsvarvning
Hårdsvarvning är en metod som kan ge lägre kostnader i jämförelse med slipning. Anledningen till detta är att hårdsvarvning kräver mindre maskinella resurser, använder standardskär, behöver mindre mängder av kylvätska och är en mer flexibel metod än slipning.
Vid slipning av en relativt enkel geometri (till exempel en cylinder), krävs det tre olika maskiner:
- Planslip
- Ytterslip
- Innerslip
Slipmaskinerna använder olika typer av slipskivor som oftast måste formas och skärpas för olika geometrier. Om produkten inte är cylindrisk och har profilerade ytor, som lagerbanor, så måste slipskivan profileras med ett diamantskärp.
Om man istället använder hårdsvarvning så krävs det normalt bara en maskin. Produkten spänns upp i en chuck eller fixeras med hjälp av en magnetchuck och därefter bearbetas den med ett skärverktyg av PCBN eller keramik. Efter första operationen måste dock produkten omspännas för att kunna bearbeta de resterande dolda ytorna.
För att bearbeta en cylinder är hårdsvarvning ett självklart val eftersom det endast krävs en bearbetningsmaskin istället för tre slipmaskiner. Avvägningen när det är lönsammare att använda hårdsvarvning gentemot slipning måste noggrant beräknas för att göra rätt investering eller bestämma tillverkningsstrategi. Faktorer som t.ex. seriestorlek och storlek på komponenterna som skall produceras är avgörande för rätt beslut.
Vid mycket långa serier och relativt små produkter kan slipning vara mera ekonomisk är svarvning. Vid val av produktionsstrategi måste man också ta hänsyn till andra faktorer som t.ex. tidsåtgång for uppspänning av komponenten. Det bör nämnas att effektiva slipmaskiner som använder centerless fixering av cylindriska komponenter kan ge mycket kortare cykeltider jämfört med hårdsvarvning.
Hårdhet
Hårdsvarvning görs normalt inte med hårdmetall. Istället används skärplattor av keramik eller PCBN därför att de bibehåller sin hårdhet och motståndskraft mot abrasiv förslitning även vid de höga temperaturer som uppstår i skärprocessen.
Bortsett från mycket små fyndigheter av meteoritiskt Lonsdaleit, har naturliga diamanter absolut högst hårdhet. Problemen med de syntetiskt tillverkade diamatverktyg som används industriellt, är dels deras sprödhet, dels att deras hårdhet minskar med ökad temperatur. Vid 700 °C börjar verktygen att angripas av syret i omgivningen och omvandlas till koldioxid. Figur 5 visar hur olika skärmaterial tappar sin hårdhet som funktion av uppnådd temperatur, där vid en temperatur på 1000 °C, ett PCBN skär har tappat ca 2/3 av sin initiala hårdhet.
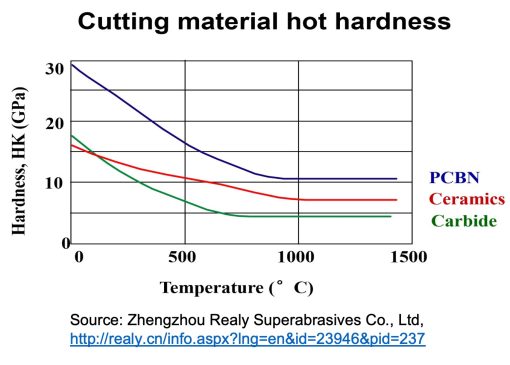
PCBN är ett verktygsmaterial som är det näst hårdaste efter diamant. Fördelen med detta material är att det kan motstå det höga kontakttryck som uppstår vid hårdsvarvning även om temperaturerna kan uppgå till över 1000 °C i kontaktzonen mellan verktyget och arbetsmaterialet.
Keramiska skärplattor har mindre slitstyrka än PCBN, men de är i gengäld betydligt billigare.
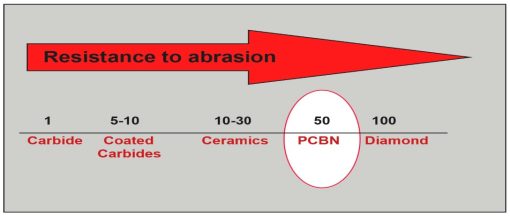
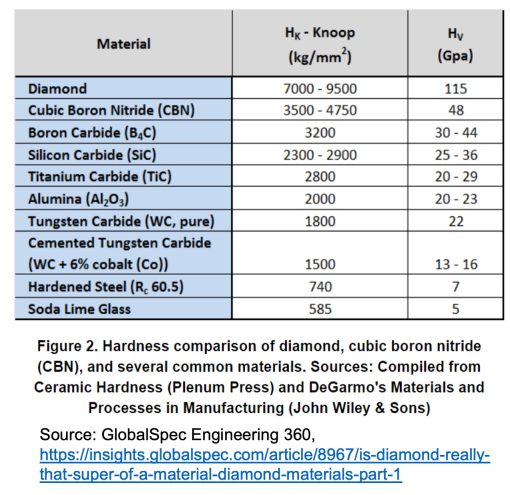
Verktygsslitage
Två viktiga faktorer som kraftigt påverkar produktionsekonomin i hårdsvarvning är:
- Verktygskostnad
- Eventuella oplanerade stopp på grund av spåntrassel (speciellt vid automati-serad produktion med begränsad bemanning)
Ett sätt att bedöma ett skärverktygs prestanda är via Taylors ekvation. Under stabila förhållanden ger ekvationen en rät linje i ett log–logdiagram (se figur 8), om man vid bearbetningstester endast varierar skärhastigheten och mäter tiden det tar att nå en viss förutbestämd fasförslitning på verktyget (exempelvis 0.10 mm). Genom att upprepa testerna med alternativa skärverktyg eller råmaterial, så får man en uppfattning om de olika varianternas kapacitet. Eftersom man vid hårdsvarvning ofta använder mycket låga skärdjup och matningar, kan det hända att vissa lokala förslitningsfenomen påverkar Taylorlinjen. Då kan det vara ett enklare alternativ att istället mäta och jämföra uppnådd bearbetad längd (SCL = spiral cut length) till ett givet förslitningsmått vid identiska skärdata.
I am text block. Click edit button to change this text. Lorem ipsum dolor sit amet, consectetur adipiscing elit. Ut elit tellus, luctus nec ullamcorper mattis, pulvinar dapibus leo.

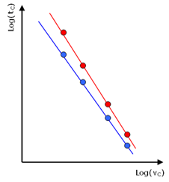
På grund av de låga skärdjup och matningar som används vid finbearbetning så erhålles inga brytspån. Skärprocessen resulterar i en mjuk spånform, som tenderar att fastna på skärverktyget eller arbetsstycket. Högtryckskylning kan förbättra spånavgången, men ett annat alternativ kan vara cykliska variationer i CNC–programmet om det inte påverkar detaljens ytkrav. Annars är det nog manuell spånrensning som gäller. Figur 10 visar hur fasförslitningen kan se ut vid hårdsvarvning och även en typisk spånform.
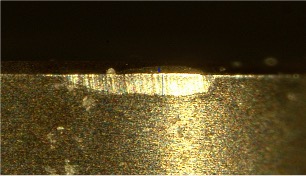
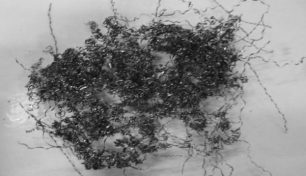
Kylmedia – temperatur i skärzonen
Temperaturen vid skäreggen kan som nämnts bli hög vid hårdsvarvning – upp till och över 1000 °C i den primära skärzonen på skäreggens spånsida (se figur 12). Temperaturnivån bestäms företrädesvis av arbetsmaterial, kylmedium och skärhastighet. Högre temperatur medför ökat verktygsslitage och temperaturrelaterade formförändringar på arbetsstycket, liksom temperaturdrift i bearbetningsmaskinen.
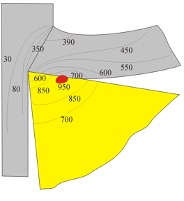
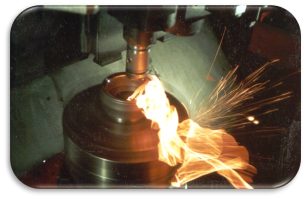
Kylmedia kan generellt indelas i fyra huvudgrupper:
- Torrbearbetning
- Minimalsmöjning (MQL)
- Normalt skärvätskeflöde
- Högtryckskylning (HPC)
Torrbearbetning kan ske helt utan någon tillförsel alls, vilket ger den största temperaturökningen, men hit räknas även kylning med tryckluft samt kryogen kylning med CO2 eller N2. Den kryogena kylningen ger störst kyleffekt på grund av temperaturer ner mot minus 30-70 °C, vilket kan innebära kraftig försprödning av skärverktyget.
Vid minimalsmörjning tillförs ca 15-25 ml/h miljövänligt smörjmedel (främst vegetabiliska oljor) blandat med luft via separat extern utrustning, vilket framför allt har smörjande effekt i skärzonen, men även kylande effekt på grund av minskad friktion.
Normal skärvätsketillförsel är ca 1500–2500 l/h med ett tryck av normalt 2–7 (10) bar.
Vid högtryckskylning slutligen, tillförs betydligt mindre kvantitet skärvätska, fast med ett tryck av 120 – 150 bar eller högre via speciella högtryckspumpar. HPC ger bättre verktygslivslängd, bättre ytor och god spånkontroll. Pumpen är dock relativt dyr och avger relativt höga dB.
Läs mer om hur hårdsvarvning kan komma att revolutionera industrin
Filmer
Hårdsvarvningsprocessen (sve)
Cutting tools for hard turning (eng)
White layer formation in hard turning (eng)
Material för kullager (sve)
Om projektet
Projektet Turn2Flex får finansiering stöd från Vinnova, Formas och Energimyndigheten genom Produktion 2030 som är ett av de strategiska innovationsprogrammen i Sverige. Projektet leds av RISE i samarbete med Chalmers Tekniska Högskola, Ovako, SKF, Skärtekniskcentrum Sverige, Slitskyddsteknik (SST) och Sumitomo Electric Hartmetall.
Projektet startades 2021-04-28 och pågår till 2024-04-26
Projektbudget: 9 250 000 SEK
Kontakta oss
Projektledare
Seyed Hosseini, RISE Research Institutes of Sweden
010-228 47 57
seyed.hosseini@ri.se
Skärtekniska experter
Jacek Kaminski, Skärteknikcentrum Sverige
072-458 06 26
jacek@sktc.se
Thord Johansson, SST Slitskyddsteknik AB
070-927 20 75
thord.i.johansson@telia.com